The precision of mold manufacturing significantly impacts the quality of the products produced, making it crucial to ensure accuracy in mold processing. Dongguan Dowell Casting Products Co., Ltd. has consistently excelled in this area by adhering to four key principles that have garnered widespread acclaim within the industry. The methods to guarantee and enhance processing precision can be summarized as follows:
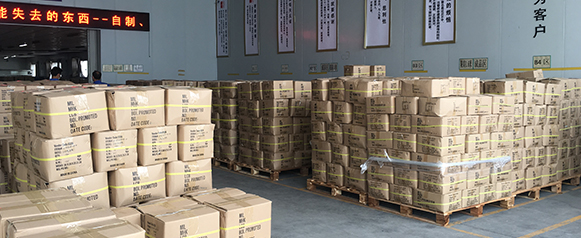
1. Reducing Original Errors
Enhancing the geometric accuracy of machine tools used for part processing, improving the precision of fixtures, measuring tools, and tools themselves, and controlling deformations caused by mechanical stresses, heat, tool wear, internal stresses, and measurement errors are direct ways to reduce original errors. To improve machining precision, it is necessary to analyze various original errors causing processing inaccuracies and adopt different measures based on the specific situation. For the processing of precision parts, efforts should focus on enhancing the geometric accuracy and rigidity of precision machine tools and controlling thermal deformations during processing. In contrast, for parts with formed surfaces, the emphasis should be on minimizing shape errors in forming tools and installation errors.
This method is a fundamental approach widely applied in production, aimed at identifying and reducing the main factors causing processing errors.
2. Compensating for Original Errors
The error compensation method involves intentionally creating a new error to offset the original errors present in the process system. If the original error is negative, the artificially introduced error should be positive, and vice versa, striving to make the magnitudes of both errors equal. Alternatively, using one type of original error to counteract another aims to achieve similar magnitudes but opposite directions, thereby reducing processing errors and enhancing precision.
3. Transferring Original Errors
The essence of the error transfer method is to shift geometric errors, force-induced deformations, and thermal deformations within the process system. There are numerous examples of applying this method. For instance, when a machine tool's precision does not meet part processing requirements, the approach often involves finding solutions in process or fixture design rather than solely improving machine precision, redirecting the geometric error to aspects that do not affect processing accuracy.
4. Dividing Original Errors
In processing, errors from previous operations or changes in workpiece material properties can lead to significant variations in original errors. This issue is addressed by adopting a group adjustment method to evenly distribute errors. Essentially, this method divides the original error into 'n' groups, reducing the range of error for each group to 1/n of the original, and then adjusting the processing for each group accordingly.