Flat injection molding parts have a large surface area, which leads to significant shrinkage. Due to the severe molecular orientation in large injection-molded parts and uneven cooling of the p pmold, the shrinkage rates in different directions vary, causing thin, flat injection-molded parts to easily deform and twist. Sometimes, when one side of a large flat part has a supporting rib, the part will inevitably bend towards the side with the rib
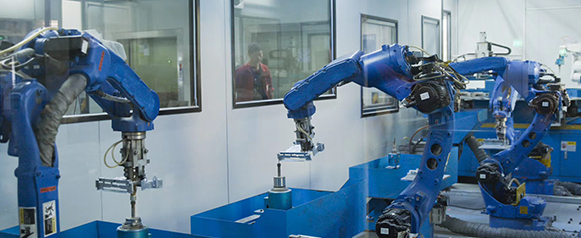
Solving the deformation problem of large flat injection-molded parts thoroughly is challenging. However, we have summarized some effective measures to address this issue:
1. Modify the Mold to Multi-Point Gates: Typically, for molds with more than 24 tons, it's advisable to use at least four gates for large flat parts. This can reduce the degree of molecular orientation and decrease the inconsistency in shrinkage rates across different directions.
2. Properly Increase Mold Temperature: For materials like ABS, maintaining the mold temperature above 60°C can reduce the cooling rate of the molded parts, minimizing deformation caused by thermal shock and lowering the degree of molecular orientation.
3. Increase Injection or Holding Pressure and Extend Time: A crucial step is to increase the injection or holding pressure and significantly extend the time to enlarge the dimensions of the molded parts, thus reducing their shrinkage. Consequently, extending the injection or holding time (by about 10-15 seconds) has become a common practice to solve deformation issues.
4. Use Post-Mold Shaping Techniques: If the above measures do not yield satisfactory results, post-mold shaping must be considered. This method requires skill as it is not commonly well-executed.
- First, eject the parts from the mold while they are still hot (should still be too hot to touch comfortably, which is critical).
- Place them on a workbench and shape them with fixtures. The design of these shaping fixtures needs to be appropriate.
- Consider the rebound of the molded parts; typically, rebound stops after about 12 hours, and the lower the ejection temperature, the greater the rebound. The principle of "overcompensation" applies, so it's essential to study the amount needed to overcompensate during production.