Bakelite, commonly known as "Caucho" and scientifically referred to as phenolic molding plastic, is a type of thermosetting plastic. It boasts high mechanical strength, stable performance, acid and alkali resistance, and the ability to withstand both high and low temperatures. The Dowell Casting bakelite injection molding process can be broken down into several key steps, which are outlined below to provide a comprehensive understanding of the process.
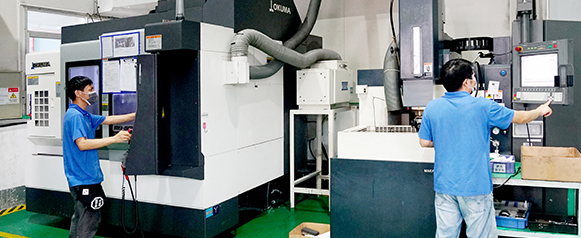
1. Heating of the Bakelite Mold:
Unlike plastic molds that can start production immediately upon setup, bakelite molds require a lengthy heating period.
2. Heating of the Bakelite Material:
The bakelite material, usually in powder form, melts through friction generated by the barrel's heating device and the screw, achieving the pre-solidified state necessary for molding.
3. Injection of the Bakelite Product:
Once pre-molding is complete, the mold closes, and the injection begins. The molten material is pushed by the screw through the nozzle and into the mold cavity via the main runner, sub-runners, and gates, filling the entire cavity. Due to the shear heating during injection and the high temperature of the mold, the temperature of the molten material rapidly increases, entering a rapid reaction state. Unlike plastic products, the injection time for bakelite products is longer.
4. Holding Pressure Cure:
Immediately following injection, the material enters a holding pressure phase. This step serves two purposes: to compensate for shrinkage and to ensure that the final product has a dense and robust structure. After holding pressure is applied, there is a delay while the material fully cures and the product takes its final shape.
5. Ejection of the Bakelite Product:
The mold opens, and the finished product is ejected. The mold is then cleaned, readying it for the production of the next item.