Bakelite injection molding, also known as bakelite forming, is a process that involves injecting bakelite powder into a mold under high temperature and pressure, then curing and cooling it to form the final product.
Bakelite injection molding offers several benefits:
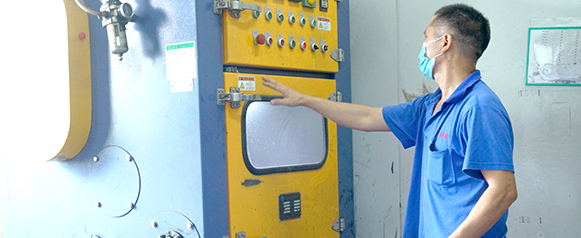
1. High Production Efficiency: Bakelite injection molding employs automated production, allowing for rapid and continuous manufacturing, significantly enhancing production efficiency.
2. Stable Product Quality: The process ensures precise dimensional control, resulting in stable product quality with a high qualification rate.
3. Complex Product Shapes: Bakelite injection molding can produce items with complex shapes and compact structures, meeting various design requirements.
4. High Material Utilization: The process achieves high utilization rates of bakelite powder, reducing material waste.
5. Energy-Saving and Environmental Protection: Closed production methods minimize dust pollution, contributing to environmental protection.
6. Cost Reduction: Large-scale production capabilities help lower production costs, enhancing corporate competitiveness.
7. Excellent Insulation Properties: Products made from bakelite injection molding exhibit excellent insulation properties, making them widely applicable in the electrical and electronics industries.
8. Superior Wear Resistance: These products also demonstrate outstanding wear resistance, extending their service life.
In summary, the bakelite injection molding process boasts numerous advantages, including high production efficiency, stable product quality, complex shape capability, high material utilization, energy conservation, cost reduction, excellent insulation, and superior wear resistance. It finds extensive application across industries such as electrical, electronics, automotive, and aviation.